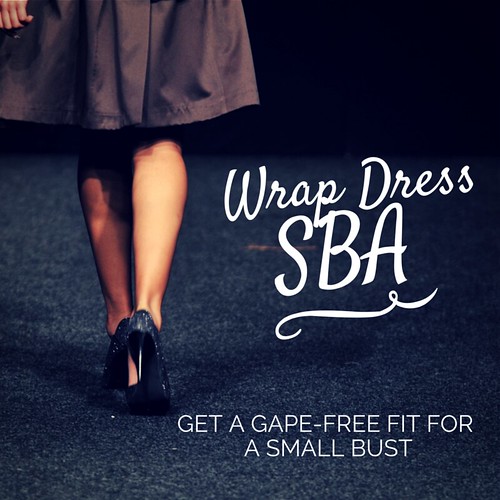
Up until a few months ago, I couldn’t wear anything with a wrap, or surplice, neckline. Being of the small-busted variety (and damn proud I might add!), wrap dresses and tops would always sag or dramatically gape open, exposing my bra (eeek!), due to the length of the wrap being too long. After searching all over the internet to find ways on how to make a wrap neckline fit and having no luck with the results, I pretty much gave up on ever being able to make or wear a wrap dress or top.
Then, I put together techniques I found from two sewing resources and hit the wrap-dress-jackpot: Power Sewing by Sandra Betzina, and Threads #168 September 2013. Both cover different ways to alter wrap necklines, but combining elements from both articles gave me the winning combination for my first wrap dress I ever made at the end of last year – I highly recommend checking out both for more information on wrap dress fitting techniques.

There’s some good info out there on how to do a full-bust adjustment for wrap necklines – if you’re looking for a great post on how to make this alteration, Ann from Gorgeous Fabrics wrote an informative tutorial on how to do a FBA for a wrap dress for the McCall’s sewalong recently.
SBA Bodice Pattern Alterations
Before cutting out your fashion fabric that you plan on using for your final dress, use a knit fabric with comparable stretch/weight as your final fabric for a test bodice. I also recommend trying out all of the below steps on a test bodice to make sure you get the fit you want before committing to using these techniques on your final wrap dress.
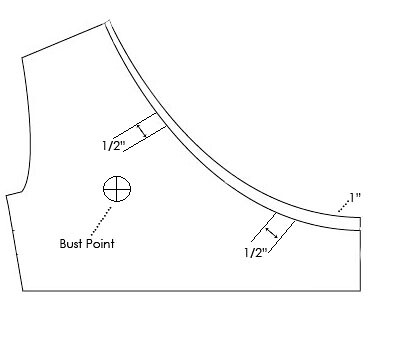
Original diagram from Sofilajantes
If you’re small-busted like me, and have tried on a wrap dress in a store, you’ve probably noticed that the length of the wrap is too long, since we don’t need as much fabric to cover our bust line. To solve, that, we’re going to take some length out of the neckline above and below the bust point by pinching out extra length above and below the bust point. This will vary from person to person, as well as pattern to pattern, so make up a test bodice to try on and play around with. For me, I ended up needing to take out 1″ of length total: 1/2″ above the bust point and 1/2″ below, illustrated above. If you need to take out more length, try to evenly distribute a series of small tucks above and below the bust point.
As a personal preference, for more coverage, I also raised the neckline. At the waist I added 1″ to the neckline, and blended it out to about a 1/2″ at the neck. This also affected the shoulder seam, which needed to be extended 1/2″.

Here’s what the pattern piece looks like after my alterations – the tucks are circled in yellow. I taped the tucks in place with scotch tape, and the tucks gradually tapered out from the tuck point. The white paper is the new drafted neckline.

Here’s another angle so you can see the tucks in the tissue a little better. The bottom tuck, on the left-hand side above, was tricky for me since it intersected with the grainline. So, I tried to keep the grainline as straight as I could while smoothing out the tissue from the tuck point.
Fixing the Wrap Gap
With the pattern alterations done, now we can move on to solving that annoying gaping problem and create a bodice that stays snug and close to the body. If you don’t have that problem with your pattern, then great! You’re ready to get sewing! If not, try out this method using 1/4″ twill tape – I like it better than using clear elastic for stabilizing a wrap neckline.
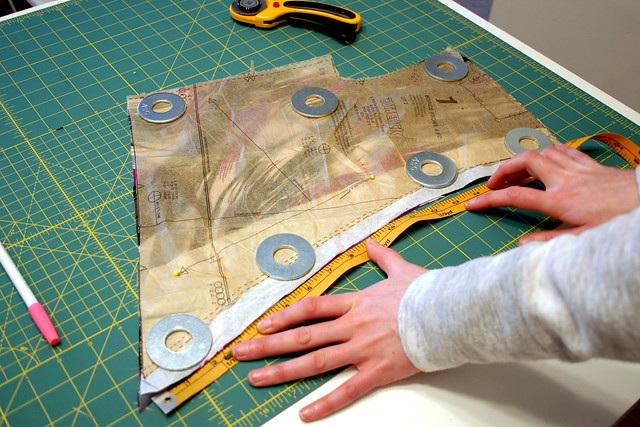
Using a tape measure or your preferred way of measuring (flexible rulers are great for this), measure the length of the neck for the front bodice piece and the neckline of the back bodice piece.

Using those measurements, cut one piece of 1/4″ twill tape that corresponds with the back neckline measurement, and two pieces of twill tape that correspond with the front neckline measurement – one for each side of the wrap. In Power Sewing, it’s recommended that if you have a B cup to cut the front strips 1/4″ shorter than the neckline measurement to draw in the neckline better. If you’re an A-lady like myself, cut the pieces out as the neckline measures.
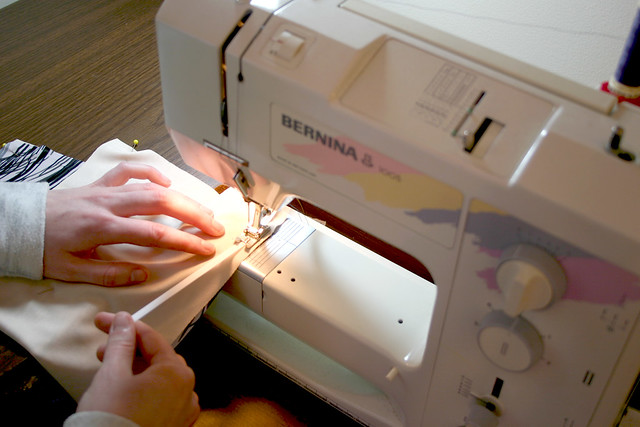
Bodice wrong side up, pin the twill tape with the edge of the tape 1/4″ away from the edge of the neckline. Using a straight stitch, sew the tape to the neckline. The feed dogs will ease in the bodice as you go, but I find stretching ever so slightly on the twill tape helps with this step. Repeat for the other side of the front neckline and the back neckline as well.

This is what one side of my front neckline looks like after stitching the twill tape. Gently press out any puckers with a cool iron.

As a personal preference, I serged the neckline edges for a clean finish after stitching all of the twill tape. When you’re at the part during dress construction where you’re ready to hem the neckline, simply turn in the neckline 5/8″ and stitch in place.
*You may have noticed in the above photos in the tutorial that the wrong side of my garment fabric looks different than the right side. Since my knit garment fabric is so sheer, I underlined the bodice with nude-colored swim tricot, so my bra won’t show through. I like the body the underlining gives the fabric as well!
There you have it – I’m now on wrap-dress #4 (and have yet to post #2-3!) using this method, and each time I’m thrilled with how the neckline turns out. If you’re small-busted like myself and have yet to successfully make a wrap dress because of how the neckline fits, I hope this opens up a world of wardrobe opportunities to you. Let me know!
Now, to finish making my dress for the sewalong…