
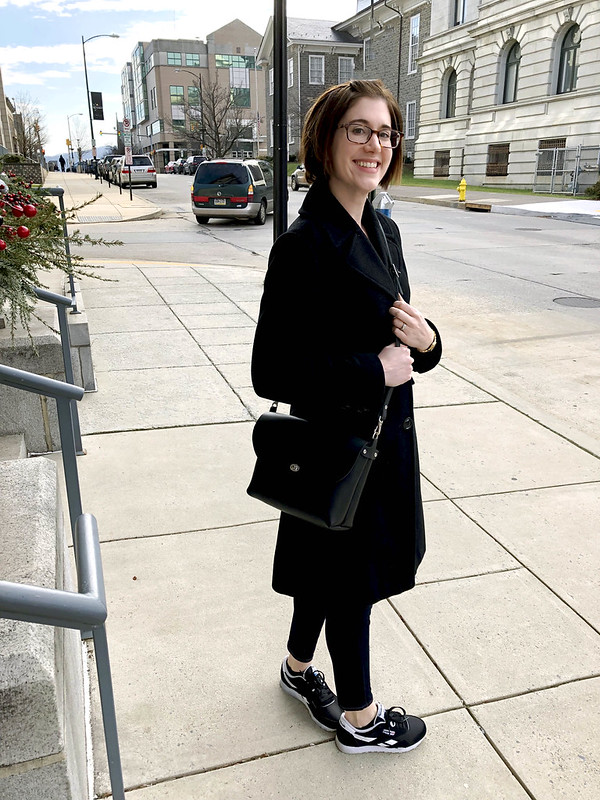
The leather-working bug is highly contagious – after making my backpack I last month, I couldn’t wait to get started on my next leather project! Especially because I have access to industrial sewing machines at my job, there was no reason to not give leather handbag making another try.
For my next project, I wanted to make a “wear with anything” black leather bag that was a simple shape but could hold a lot when running errands or travelling. I scoured patterns online and available on Etsy and stumbled across this shop, which offers a lot of very simple but classic patterns. All of the patterns are designed to be hand-sewn, which is a great option if you don’t have an industrial sewing machine that can power through thick leather.

Over the past year I collected a few pieces of leather as I dabbled in sandal making, and had just enough of a black piece of 5oz cowhide left over to cut out the main body of the bag in one piece instead of two and needing to sew a seam in the bottom of the bag. It’s a firm piece of leather that’s thick enough to hold the shape of the bag nicely without being too soft.
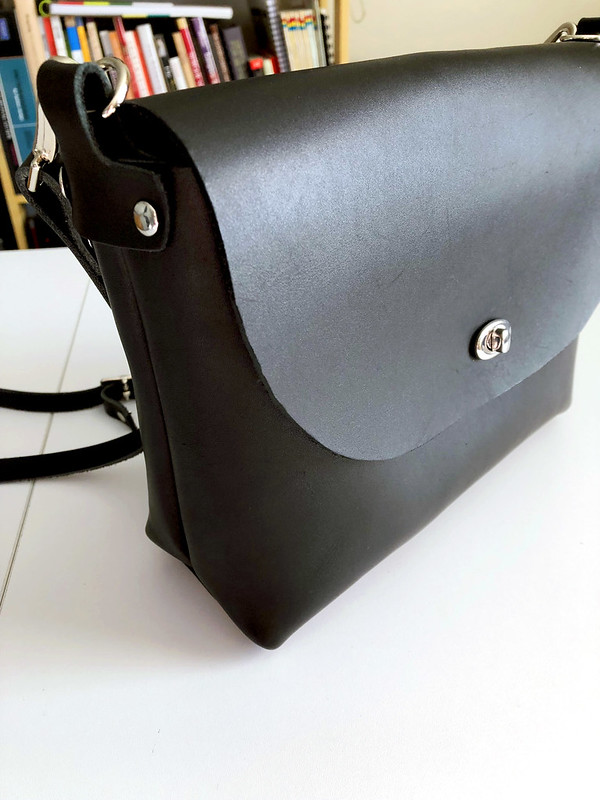
I followed the instructions for the pattern for the most part, but they were a bit on the vague side of things and didn’t properly explain how to finish the raw edges of the leather, what size hardware to buy, etc. I found all of my hardware at my local Tandy Leather: turn lock, d-rings, halter snaps, and rivets. I also picked up a piece of leather strapping for my bag instead of cutting out a strap from my leather, but I think I’m going to replace it with something else because the leather is a bit on the thick side and I’d rather use something that is a little more flexible. Plus, the raw side is exposed underneath and unfinished, which is starting to wear.
Installing the turn lock was a bit challenging since I don’t have a nice punch to cut out an even hole, so I had to use my utility blade and a bit of trial and error with inserting the lock to make sure enough of the leather was removed for the post to go through the opening and close properly.
For the flap of the bag, I used two coats of Fiebing’s Edge Kote to give the leather a bit of a more polished look. For whatever reason, I thought to only do this on the flap but not the rest of the leather pieces that have exposed raw edges, like the d-ring carriers, top edge of the bag, and the outside pocket on the back of the bag. Oh well, live and learn! I’m also not 100% sure if this was the best type of edge paint for this leather, or if I should have used something like Vernis edge paint to get a more “finished” looking edge. Will have to play around with that and experiment! After finishing the edges of the flap, I sewed it on to the back of the bag.
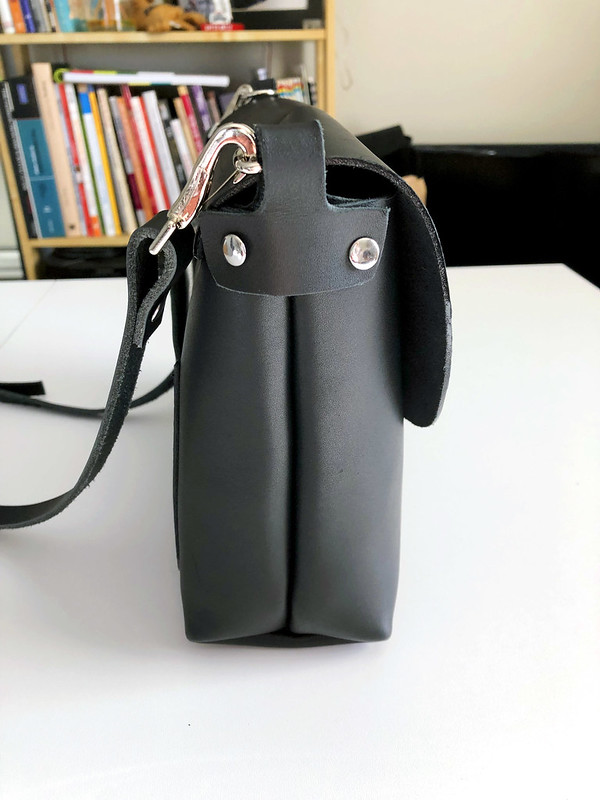
The body of the bag was assembled wrong side out and then flipped out after the sides and corners were sewn. Boy, it was a wrestling match to get this leather flipped right side out and the corners pushed out. In retrospect, I should have skivved the edges of the bag before sewing to reduce the bulk, but the skivving machine wasn’t functioning properly when I had sometime to use the machines at work so I had to forgo using it. I was so nervous that I wouldn’t be able to power through two layers of 5oz leather and intersecting seams with the Juki industrial machine, because I didn’t skive my leather, but that baby sewed right through it like butter!
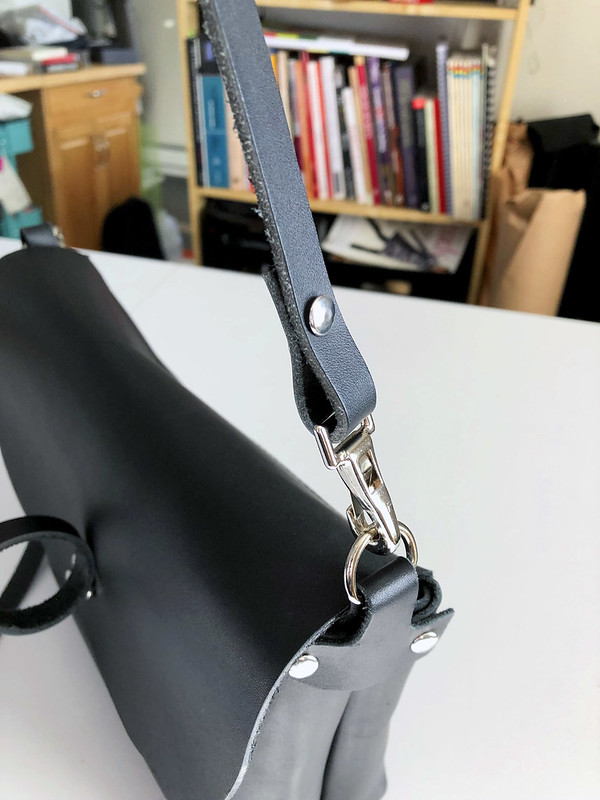
After work that night, I assembled the d-ring carriers and the strap onto my bag. Truth be told, my rivets are a bit on the wonky side – the posts were too long and I didn’t realize it when I bought them. This meant that when I hammered my rivets into the leather to hold the d-ring carriers and the strap ends together, the metal post bended and they don’t go through my bag or strap straight. I bought these rivets purely based on the size of the head of the rivet and not the post length, d’oh! Again, leather working newbie mistake.

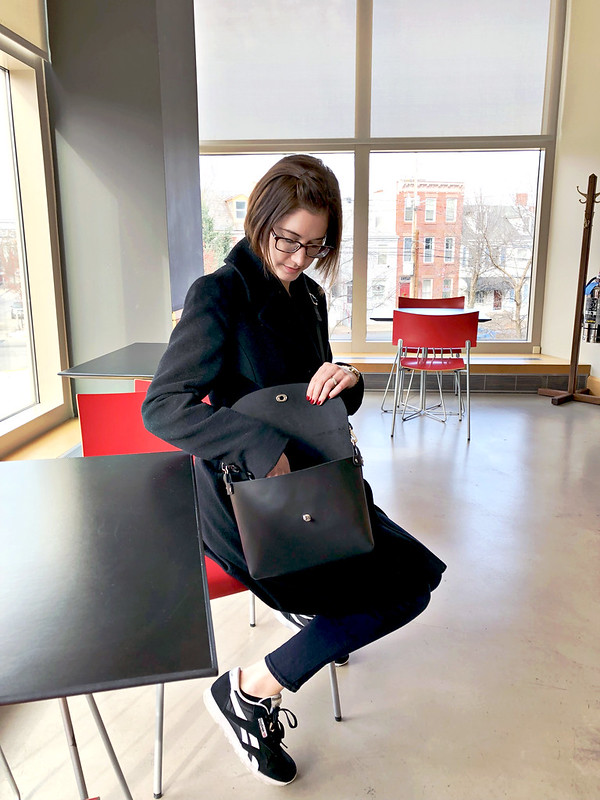
I love how roomy and spacious this bag is – I had my wallet, leather clutch with my makeup, gloves, keys, and a Kindle inside the bag with no problem during my trip to PA to visit my family for Christmas . It’s a great bag for traveling.

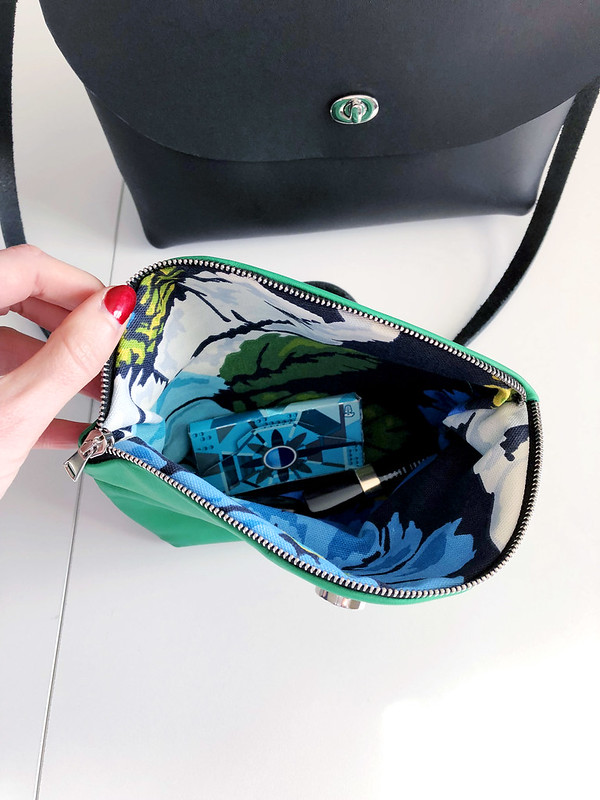
I also made an Ida Clutch out of a green Italian lamb hide the day before we left on our trip. It’s such an easy sew, I whipped it up in a couple of hours in the afternoon. The only issue I had was inserting the zipper, the leather stretched out a bit since I couldn’t use my walking foot to get close to the zipper and had to use my zipper foot. I also didn’t have any snaps handy like the pattern calls for, so I used a magnetic snap instead for the closure.
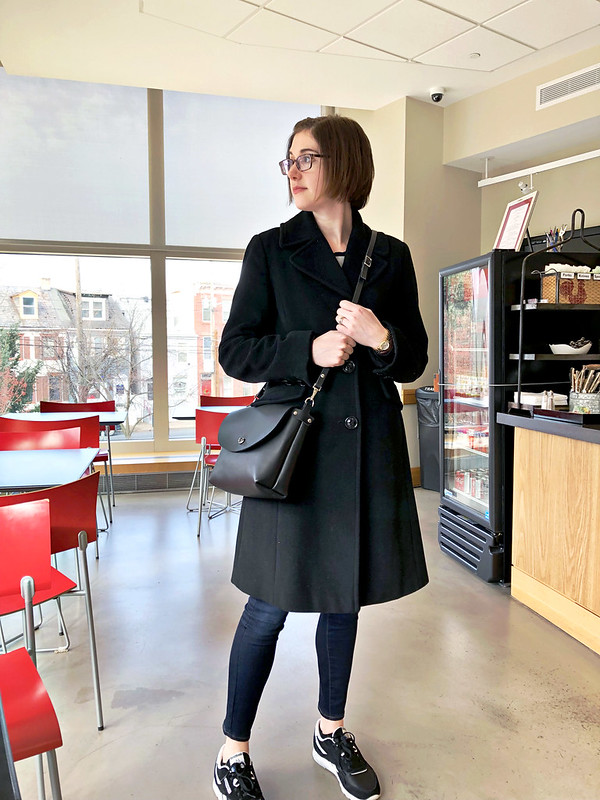
Next up I have a soft brown leather tote bag in the works and I’m planning my next shoe designs – I’m heading to London in about a week for a 3-day shoemaking workshop!
Leather: Cross-Body – cowhide, Ida Clutch – lamb
Patterns: Cross-Body, Ida Clutch
Hardware: Tandy Leather
Sewing Machine: Juki LZ-2280A